our workplace
How we make it
01.
Raw Wool
Wool is thoroughly sorted to remove any undesirable materials before being imported or purchased from surrounding marketplaces. Wool frequently contains oil and dust, which are removed by giving it a good wash before letting it air dry for two to three days.
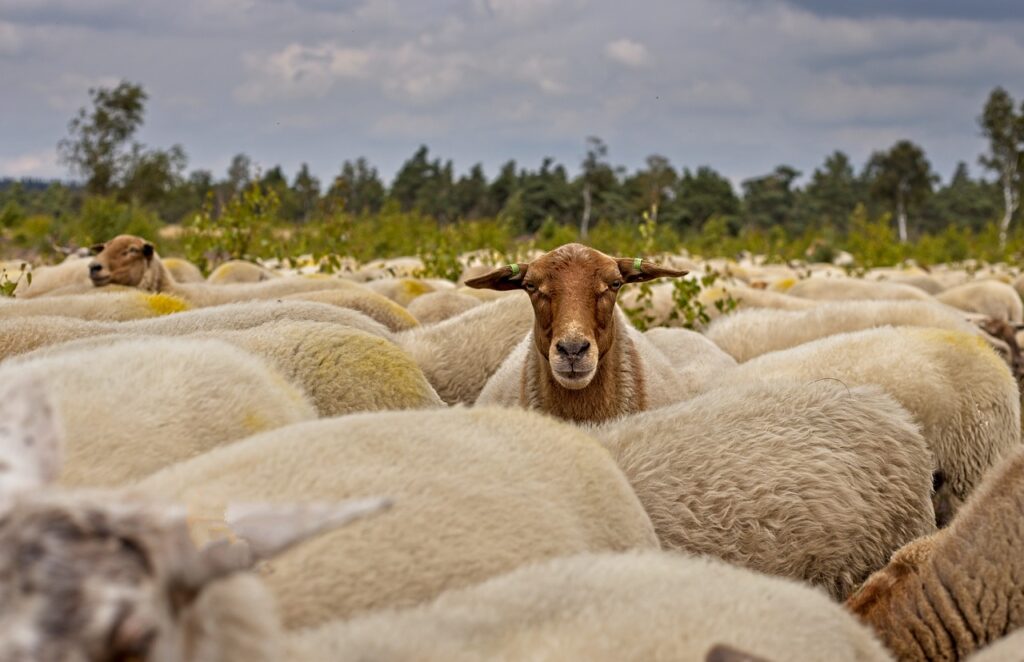
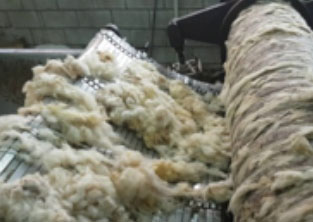
02.
Scouring
It is the cleaning of woollen fibre. Wool fibre contains a lot of dust, grime, and an oily, sticky substance known as suint. Suint is a wax-like substance that sheep sweat glands release. To get rid of suint, the fibre must be rinsed with caustic.
03.
Woollen Yarn Spinning​
In spinning, there are two steps. Carding and Spinning: Carding can occasionally be done by hand with a carding brush or on manually-operated carding rollers. Using a charkha or a spinning wheel, the carded wool is spun into yarn. The thickness of the yarn is determined by the carpet’s quality; typically, a three-ply yarn is utilised.
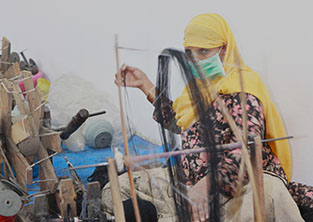
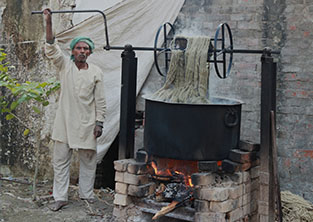
04.
Yarn Dyeing
Machine dyeing in enclosed Chambers has essentially taken the role of the conventional pot dyeing technique. It is forbidden to use dyes that include dangerous ingredients like AZO; instead, reputable worldwide manufacturers’ dye products are used. These colours offer excellent fastness. The dyed yarn must be dried in the sun for one to three days, depending on the weather. Some producers continue to employ vegetable (natural) dyes and pot dyes.
05.
Yarn Opening or Reeling
is a process that involves opening the bigger and loose lea and wrapping it into tightly wrapped bunch which is smaller in size
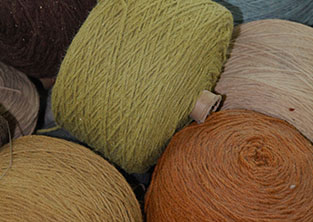
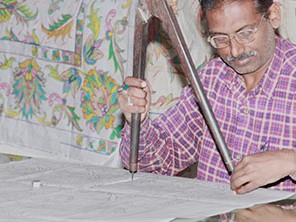
06.
Designing
Curvilinear, geometric, and figural patterns are sometimes separated into three groups when discussing patterns used in carpet manufacture. We shall highlight a few of the most prevalent named patterns out of the numerous that are frequently seen.
07.
Raw Washing
It is done as the first wash to clean the carpet and for removal of dust and dirt or any stains on the carpet.

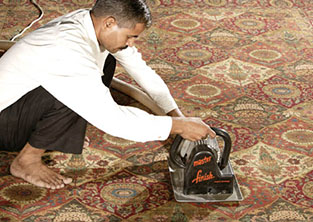
08.
Shearing
After carpet is washed the piles are cut to level them to same height. This is called Shearing.
09.
Embossing
is the process of trimming the design’s carpet border, which provides the motif detail. It can also be accomplished by lowering the pile height of heaps other than motif piles.
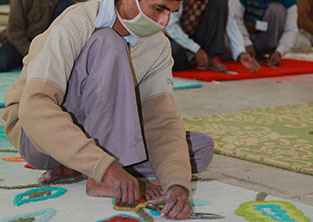
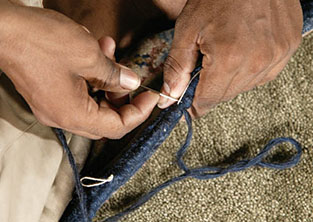
10.
Side Binding
The sides of the carpet is bound by a separate thread which is a thick thread and often doubled. This gives additional strength to the carpet.
11.
Seinging
it is the process of burning the protruding fibres on the backside of the carpets. This gives a sharp and neat finish to the carpet.
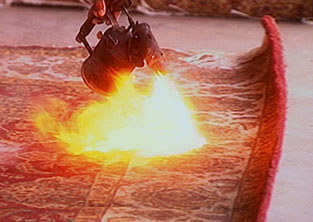
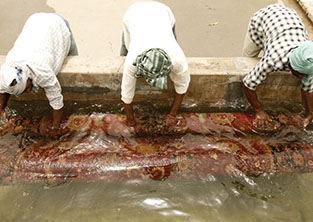
12.
Final Washing
The carpet is washed for the final time. Final washing provides it the required luster.
13.
Drying
in traditional setup dyeing is done under the sun, but many manufacturers have drying machine which can control the tempreature and moisture of the carpet.
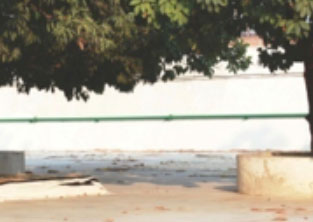
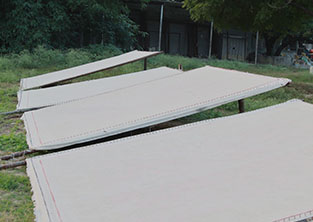
14.
Stretching
Stretching is done to make the sides straight otherwise the carpet has some curved edges .
15.
Final Clipping
This is the finishing step in the manufacturing of carpet. The clipping is done with minute detailing.
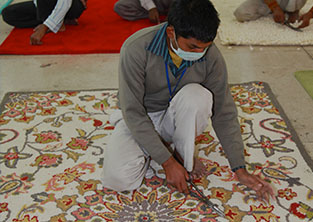
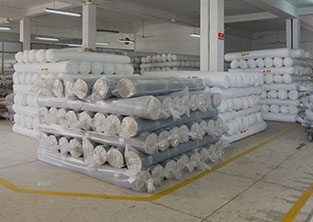
15.
Packing and Bailing
After the carpet is finished, it is packed and bailed for exports.